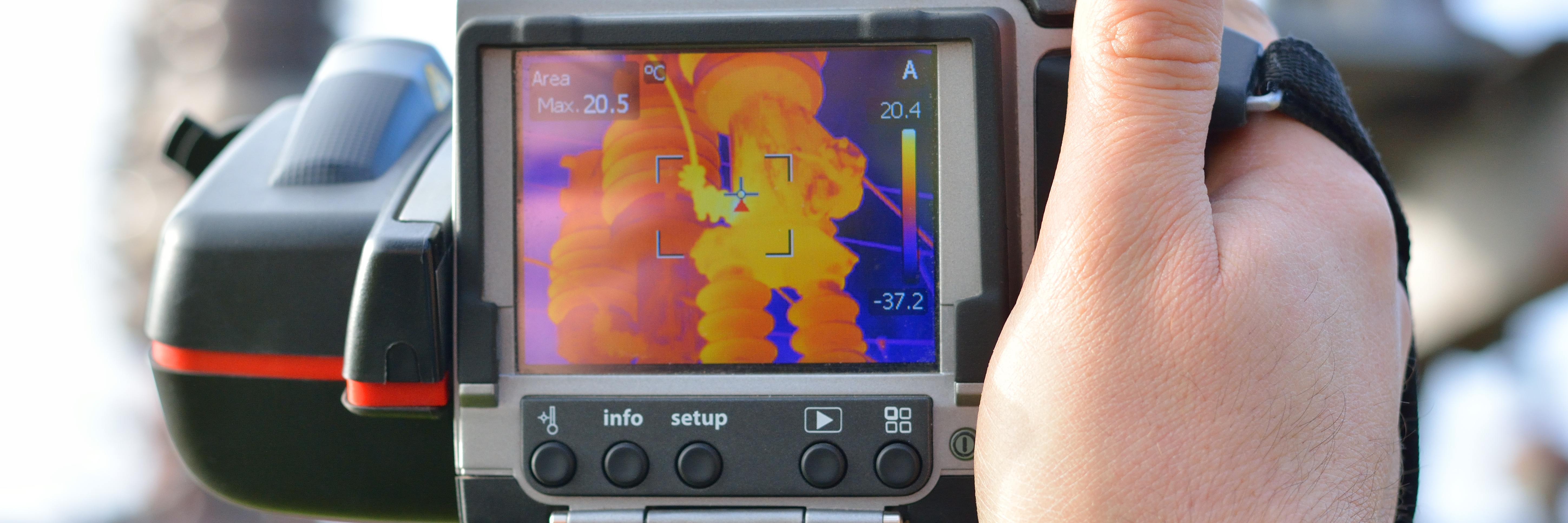
Infrared thermography
properties.trackTitle
properties.trackSubtitle
More than meets the eye
An infrared survey can help keep small issues from becoming disasters. Repairing a loose connection– easily found with a thermographic scan – might cost only $100. If undetected, that same connection could result in a fire. That might mean injury, loss of life or damage that makes the whole building unfit for occupancy and shuts your business down.
Thermographic scans are a wise investment. Industry sources show that the monetary savings they produce can be 20 times as much as the initial cost of the survey. This does not include the potential losses due to damage associated with fire.
How infrared thermography works
All electrical and mechanical equipment radiates heat. Infrared video cameras that are sensitive to this thermal radiation, detect and measure the temperature differences between surfaces. The cameras then convert the information and display it as an image visible to the human eye, allowing us to “see” a heat signature.
Abnormal or unexpected thermal patterns typically indicate a problem with the equipment, including conditions such as:
- Loose electrical connections
- Overloaded circuits or phases
- Deteriorated or damaged insulation
- Bearing failure
- Insufficient lubrication
- Steam leaks
These and other issues show up as hot spots that a trained professional can interpret to determine the likely cause and potential remedy.
Real-world examples of effective thermography surveys

Overheated transformer bushing
This transformer experienced an internal problem that manifested itself as an overheated bushing. Within 24 hours, it was removed from service and the back-up unit was installed. This averted potential spoilage of millions of dollars in agricultural products.

Under-lubricated motor bearing
This motor read 245 degrees F, which is more than 100 degrees above specifications. Upon examination, it was discovered that the lubrication was insufficient. Correcting the problem prevented failure of the motor.

Hot meter
A small temperature rise could mean big money. An abnormal temperature rise on a conduit was detected. The local utility investigated and found the meter had been wired incorrectly at installation resulting in erroneous readings. This resulted in the local utility issuing a $60,000 credit to the facility for several years of incorrect meter readings.